Bentonite Slurry Transfer Pumps for Tunnel Construction - Case Study
What is Bentonite?
For this case study we'll be looking at the needs of a client within the infrastructure construction sector, and the challenges faced with boring tunnels and bentonite.
Before we talk about the clients’ requirements let’s explain bentonite and its use. Bentonite (also known as bleaching clay) is a naturally occurring clay used within a variety of construction applications such as tunnelling, piling, foundation works and the construction of ventilation shafts.
Used as a lubricant in drilling and tunnelling applications for cutting tools and drilling equipment, it helps to remove cuttings from drilling equipment by absorbing small particles and water within the bentonite exerting hydrostatic pressure within excavation walls.
Its unique properties enable it to absorb water up to 10 times its weight, without affecting its consistency. It can be reused many times before being cleaned via filter presses for reuse.
When pumped into excavations it helps to prevent the collapse or failure of any structure formed in unstable soils or ground which may be close to aquifers, and in soft rock within geological explorations.
It can also be combined with other materials such as cement to form a grout, which is then used in tunnel boring machines during construction operations. This is where our client requirements come in.
A Clients’ Aging Progressing Cavity Pumps
Our client contacted us who were looking to replace two ageing progressing cavity pumps installed within a tunnel boring machine (TBM) being used for the construction of railway tunnels 8Km and 16Km long. Their existing pumps had reached the end of their life and the contractor was exploring options - whether to replace their pumps with the same brand or alternatives.
Replacing the existing pumps with direct replacements meant extended lead times, and the customer wanted to adjust their process and determine whether changes in the pump could help them with their new requirements which had changed since original supply of the pumps.
One improvement the client wanted was a wider range of flow from 2M³H, to 32M³H whilst maintaining flow across pressures up to 10 bar. This would mean modification to the existing motor specification, with an inverter driven motor and extra fan cooling to allow enough turndown to meet low flow requirements.
Clients’ Tunnel Boring Operations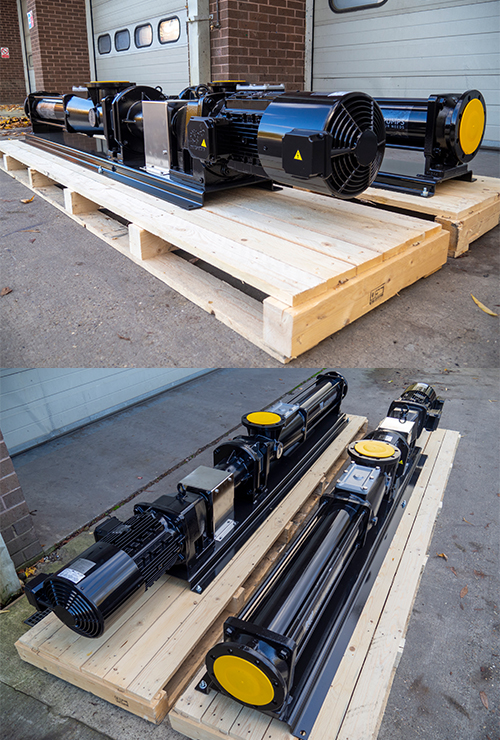
Bentonite is pumped in front of a tunnel boring machines cutter head, used to bore tunnels where conditions can vary depending on the phase or location requiring excavation. Soils can range from being clay or solid in nature, to loose or shale like, contain gas or be under high pressure as is the case under large bodies of water such as in the channel tunnel.
Bentonite conditions soil during excavation absorbing small cuttings removed by the cutter head and regulates pressure at the front of the machine to balance the earth, soil, and water pressure experienced by the cutter.
When boring, tunnelling machines create two chambers – an excavation chamber and working chamber. Bentonite flow is regulated into these chambers via progressing cavity pumps and ball valves ensuring the pressure seen at the front of the machine is balanced.
Bentonite completely fills the excavation chamber and fills around two thirds of the working chamber fed through individual 2” lines via a rotary coupling. Once bentonite has lined tunnel walls, concrete ring segments are then installed stabilising the structure. Viscosity can be up to 24,000cps, but in this application it was only around 100cps.
The Replacement Solutions
We specified and selected two DN125 - 5” Horizontal Progressing Cavity Pumps from our JN range, capable of handling up to 600M³H, and pressures up to 48 Bar.
This design of pump is built differently to other designs, as its operation is supported by a separate robust bearing housing which bears the load during heavy duty pumping operation, as opposed to other models where the radial forces can be absorbed by the motor bearings. It is also built with an oversized inspection port for easy inspection of blockages and object clearance without disassembly.
The casings were manufactured in cast iron; however, the rotors were cast in AISI420B – a hard-wearing stainless-steel variant enabling the pumps to withstand wear against any solid or abrasive particles which the pump may encounter. An oversized pump meant that solids up to 46mm could be accommodated, and with a pump rotation speed between 38 – 260rpm meant that wear would be minimal. The pumps were assembled and delivered within 12 weeks
If you have an application involving the transfer, circulation, or injection of viscous solid laden liquids, speak to us to see how we can help.