Feed Pump for Demineralized Water – A Client Case Study
Horizontal Multistage Boiler Feed Pump for Demineralised Water
Boiler feed pumps are designed to feed steam generators, such as a boiler or reactor with a precise amount of feed water, to deliver a specified amount of steam which is often measured in tonnes per hour.
Also known as feed pumps, they are designed to handle water which has been treated or demineralized at high pressures and temperatures but at low flows.
Boiler feed pumps operate in one of the most demanding of applications, which can be 24/7, with low inlet pressures where if not carefully controlled can be subject to cavitation.
A distillery in Asia contacted us who were looking to upgrade their boiler and replace their aging multistage design with one of higher output of flow and pressure. They were currently feeding a boiler with demineralised Water at temperatures up to 125°C and needed a higher output of steam, meaning their current unit required upgrading.
They required a duty point of approximately 60M³H, with a pressure of over 400M Head. They wanted to operate the pump at a range of capacities to match their steam demand which fluctuates during production, meaning any unit selected needed to be suitable for operation via a Variable Frequency Drive (VFD) to alter the units speed to match their system needs.
Deionised Water and Boiler Water Treatment
Boiler Feed applications often use treated or demineralised water. Boiler water is treated to prevent scaling by controlling the alkalinity of water as well as its conductivity. A steam boiler consists of a series of boiler tubes housed within a large, pressurized vessel. A feedwater pump is used to continuously deliver water through the tubes, which is then heated to produce steam.
If water composition is not controlled it can lead to blockage, a reduction in efficiency and quality of steam, as well as corrosion of the tubes which are very difficult to replace and clean. If conductivity of the boiler feed water is too high due to the concentration of dissolved solids, this too can increase corrosion. Demineralised water is used in boiler feed applications as it is virtually free of minerals.
As steam is produced inside a boiler, water particles accumulate which condense and are salvaged via a condensate return to reuse as boiler makeup water. As condensate cools it is possible for dissolved gases to be present, consisting of CO² or Oxygen which can cause severe corrosion in boiler tubes, pipework, and associated parts. Consequently, these are removed via de-aeration devices, chemical scavengers and through demineralisation.
Due to the heavy-duty requirements of the application, there were various technical considerations required to ensure any unit selected would provide the longevity demanded by the application.
There were 3 main technical points of concern in this application:
Balancing of axial thrust
Management of NPSH
Pump Protection & Control
Balancing Axial Thrust & Thrust Bearings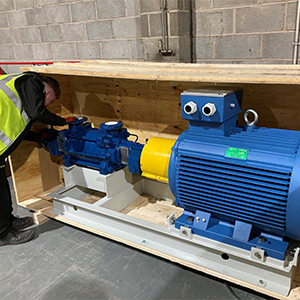
In centrifugal pump design and in particular when a unit is operating at high pressures or across a range of duties, a potential issue that can arise is the balancing of axial thrust.
Axial thrust is created in a pump by an uneven pressure distribution, which can occur at the front and back of an impeller, or in a series of impellers in a multistage pump.
It is managed in heavy duty applications by ensuring that each impeller stage is hydraulically balanced, a bush is used in the discharge casing to absorb such forces and that any remaining forces are absorbed by a thrust bearing located at the discharge end of the pump casing.
Inferior designs of multistage pumps may have bearings at one end of the pump casing or solely rely on the motor bearing for balancing such forces, however these designs are more commonly used in agricultural or domestic applications and are not suitable for use in 24/7, and high pressure boiler feed applications which is a critical application.
NPSH in Boiler Feed Applications
Due to condensate being returned to the boiler feed water, and the high temperatures of boiler feed water (125°C) being above the natural boiling temperature of water (100°C), one common problem can be cavitation of the pump due to insufficient Net Positive Suction Head (NPSH) Available which is less than the NPSH Required (NPSHr) by the boiler feed pump.
Boiler water is pressurised to enable the water to be heated above 100°C and remain liquid without vapour or steam being present in the pumped liquid.
Low NPSH pumps are a necessity in boiler feed applications to prevent premature failure of components. The clients existing unit had an NPSH requirement (NPSHr) of 3.5M, and although our flow and pressure were higher than their existing model, the design selected had an NPSHr value of only 3.2M even though the pump was operating at 60hz and at full speed - 3560rpm.
Automatic Recirculation Valve for Pump Protection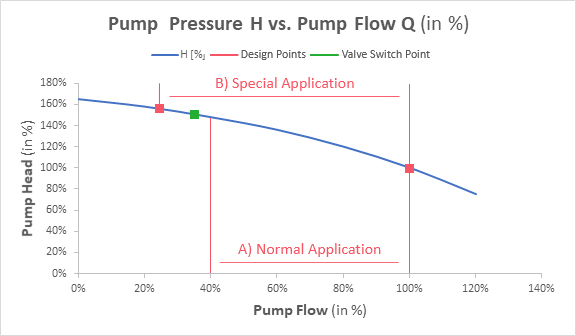
A recirculation valve automatically maintains the safe minimum continuous flow required by the pump ensuring when its speed is reduced, that the unit receives sufficient flow for effective cooling protecting the unit from overheating, vibration and cavitation.
It operates by detecting when the main delivery flow falls below a set value, causing the valve to open its bypass thus maintaining the minimum required flow delivery to the pump suction, even if the output flow stops. Once flow rises above the determined range, the bypass closes leading to outlet flow to increase.
As flow is modulated, it remains constant and as it acts as a control valve water hammering is avoided, pulsations are avoided and dampened due to the throttling effect on flow which also stabilizes flow when operating in a partial flow range.
As a result of this modulated control, the sum of delivery flow and minimum volume remains approximately constant. Typically, an automatic pump protection valve is designed for operation between 40% to 100% of volume flow. As such valves operate within a closed loop application, with suction and a recirculation line back to tank careful consideration should be given to the materials chosen to minimise corrosion under high velocity conditions.
In summary the 4 benefits of an Automatic Recirculation Valve are:
Flow is measured and modulated
The recirculation Valves Acts as a Check Valve preventing water hammer
Bypass Operation is Automatic
Bypass pressure and flow is reduced without cavitation
We recommended that the pump be fitted with an automatic recirculation valve to ensure longevity of operation.
Outcome
North Ridge specified and supplied a horizontal multistage pump designed in materials to accommodate the demineralised water at temperatures up to 125°C, delivering over 60M³H, at pressures over 400M.
The multistage pump consisted of 5 stages, with the radial double curved cast Stainless Steel impellers housed within the several stages sealed by O Rings, held in place via external tie rods.
The axial thrust from the impellers was not only hydraulically balanced at each stage, but a discharge bush in the discharge casing helped absorb axial forces, with any remaining axial thrust absorbed by the main angular and ball bearings.
The unit contained 4 bearings in total for heavy duty operation which consists of 3 angular ball bearings and 1 roller bearing. The pump was supplied with the driveshaft supported by Oil lubricated bearings kept cool by an integrated oil cooling fan.
The unit was coupled to a 160Kw IE3 High Efficiency Motor suitable for variable speed operation with a bearing insulated at the non-drive end (NDE Insulated), preventing circulating current from flowing via the inner race of the bearings, its bearing balls, or rollers to the motor frame which can occur during variable speed operation due to the harmonics present at various frequencies.
The unit was manufactured in under 14 weeks and packed to ISPM15 before being shipped via Sea freight at the clients request to Asia.